The Art of Manufacturing Umbrella Head Roofing Nails with Washers
The manufacturing process of umbrella head roofing nails with washers is a meticulous art form that requires precision, skill, and dedication. These specialized fasteners are an essential component in the construction industry, particularly for securing roofing materials such as shingles or metal panels. The unique design of the umbrella head, combined with the functionality of the washer, provides superior holding power and prevents water infiltration, making them invaluable in ensuring the integrity and longevity of roofs.
The process begins with selecting high-quality raw materials, typically stainless steel or galvanized steel, which offer excellent corrosion resistance and strength. The steel wire undergoes a drawing process to achieve the desired diameter and length for the nail shank. Each step is carefully monitored to maintain consistency and quality standards.
Next, the nail shank is fed into a heading machine, where it is cold-formed into the characteristic umbrella head shape. This operation requires precise timing and pressure to ensure that the head is uniform and securely attached to the shank. The size and angle of the head are crucial; they must be large enough to cover the shingle or panel but not too cumbersome to handle during installation.
Concurrently, the washer is stamped from a sheet of metal, often using automated presses that can produce thousands of washers per hour. These washers are designed to fit snugly around the nail shaft, just beneath the head These washers are designed to fit snugly around the nail shaft, just beneath the head
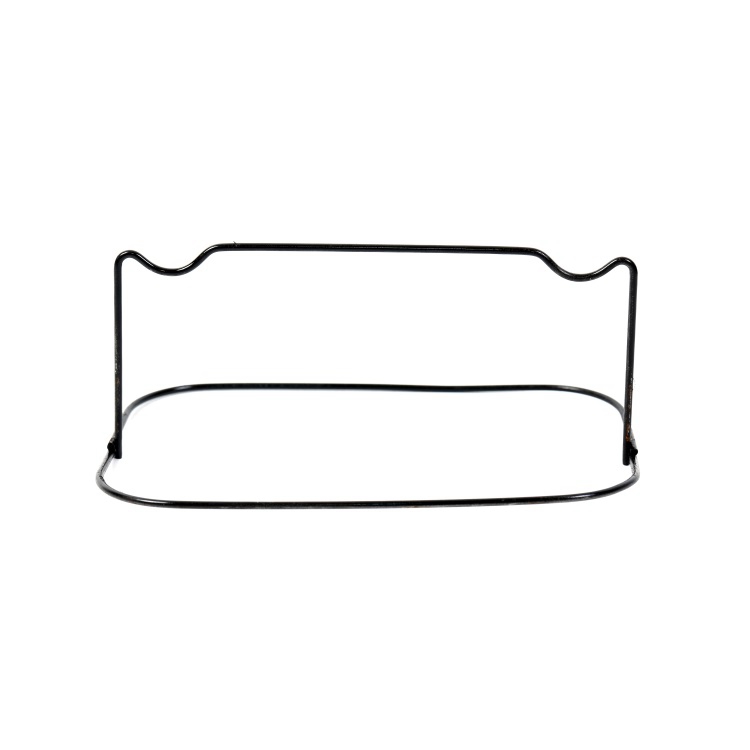
These washers are designed to fit snugly around the nail shaft, just beneath the head These washers are designed to fit snugly around the nail shaft, just beneath the head
umbrella head roofing nails with washer manufacturer. They serve as a barrier, preventing the roofing material from directly contacting the nail head and reducing the risk of tearing or damage during high winds or other extreme weather conditions.
Once the nails have been headed and the washers stamped, they are brought together in an assembly line. Workers or automated equipment place each washer onto the nail shaft, ensuring a secure fit. Some manufacturers may also apply a coating to the nails at this stage, such as zinc plating or a protective paint, to further enhance their durability and resistance to the elements.
Finally, the completed umbrella head roofing nails with washers are packaged carefully, often in bundles held together by plastic ties or wire, and labeled for shipping. Quality control checks are performed throughout the packaging process to ensure that only products meeting the highest standards are sent to distributors and, eventually, to construction sites worldwide.
In conclusion, the manufacture of umbrella head roofing nails with washers is a testament to the ingenuity and craftsmanship inherent in the building materials industry. These nails, though small in size, play a significant role in the stability and protection of our buildings. As technology advances and new materials emerge, the methods of producing these vital components may change, but the underlying principles of quality, strength, and reliability will undoubtedly remain constant.