Understanding Galvanized Welded Wire Mesh Rolls A Comprehensive Guide from the Factory Perspective
Galvanized welded wire mesh rolls, a staple in various industries, are manufactured through a meticulous process that combines precision engineering with robust material science. This article delves into the heart of the matter, offering an inside look at the factory production of these essential construction and agricultural materials.
A galvanized welded wire mesh roll is essentially a grid-like structure made from steel wires, which are interconnected through a welding process. The primary feature that sets it apart is its zinc coating, which provides exceptional corrosion resistance, making it ideal for outdoor applications.
The journey begins in the factory where high-quality steel wires are sourced. These wires are initially straightened and cut to the desired length. The wires are then fed into advanced welding machines that use electric current to fuse them at each intersection, creating a durable mesh pattern. This process, known as resistance welding, ensures a strong, consistent bond without the need for additional adhesives or fasteners.
After the welding process, the mesh is then immersed in a bath of molten zinc. This is the galvanization stage, where the zinc coating forms a protective layer over the steel, safeguarding it against rust and environmental degradation. There are two main types of galvanization hot-dip and electro-galvanization. Hot-dip involves dipping the mesh into a pool of molten zinc, while electro-galvanization uses an electrical current to deposit zinc onto the wire surface. Each method offers different benefits, with hot-dip providing a thicker, more robust coating and electro-galvanization offering a smoother finish Each method offers different benefits, with hot-dip providing a thicker, more robust coating and electro-galvanization offering a smoother finish
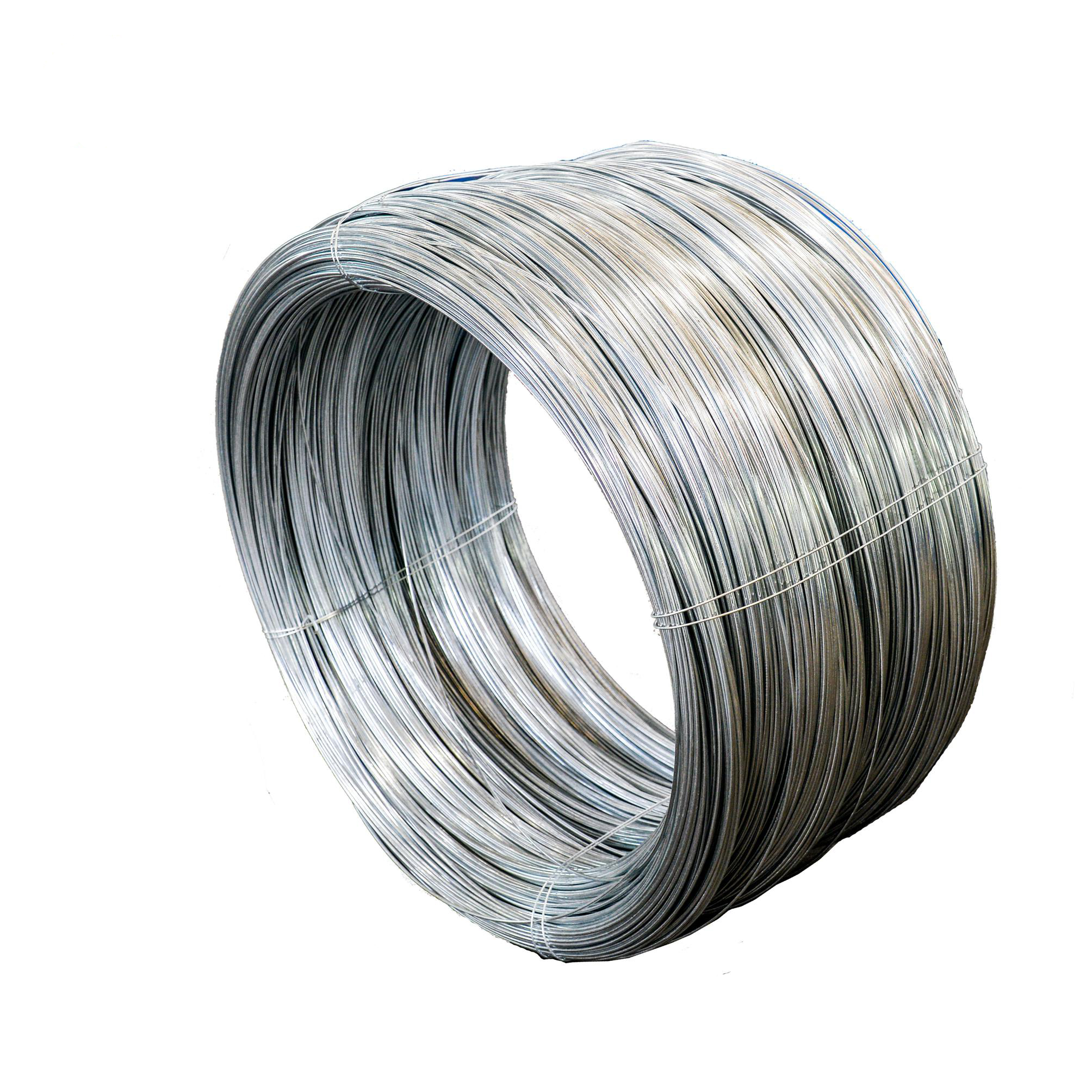
Each method offers different benefits, with hot-dip providing a thicker, more robust coating and electro-galvanization offering a smoother finish Each method offers different benefits, with hot-dip providing a thicker, more robust coating and electro-galvanization offering a smoother finish
galvanized welded wire mesh roll factory.
Once the galvanization is complete, the mesh is allowed to cool and solidify. It is then rolled up, forming the familiar cylindrical shape that makes it easy to transport and handle on site. Quality control is a critical step, with each roll inspected for consistency, strength, and adherence to industry standards.
In the factory, efficiency and safety are paramount. Modern factories utilize automated systems and robotics to streamline production, minimize waste, and ensure worker safety. However, human expertise remains crucial in monitoring the quality of the final product and adjusting the manufacturing process as needed.
Galvanized welded wire mesh rolls find usage in a myriad of applications, from fencing and animal enclosures to construction and industrial filtration. Their versatility, durability, and cost-effectiveness make them a popular choice worldwide.
In conclusion, the production of galvanized welded wire mesh rolls in a factory is a blend of traditional craftsmanship and cutting-edge technology. From the selection of raw materials to the final inspection, every step contributes to the reliability and longevity of this versatile product. As technology advances, we can expect even higher levels of precision and sustainability in the manufacturing of these essential wire mesh rolls.