The concrete nail producing line is an essential asset for manufacturers seeking to tap into the construction industry's robust demand for high-quality, durable nails. This particular production process stands out as a pinnacle of technological advancement, combining precision, efficiency, and innovation to support large-scale manufacturing needs. Here’s a deep dive into how this production line operates and why it is pivotal for businesses aiming to establish authority and trustworthiness in the industrial space.
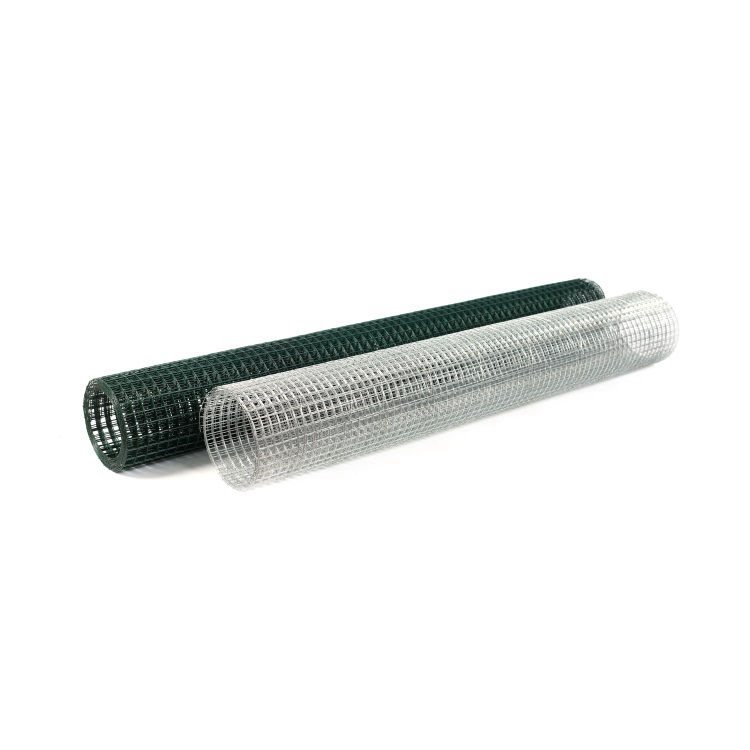
Concrete nails, distinct from regular nails, are specifically engineered to penetrate hard materials like concrete and masonry. Their production involves high-grade steel, ensuring the nails' durability and strength, which are critical for construction applications.
The concrete nail production line optimizes this process through several advanced stages.
Firstly, the raw material, usually high-carbon steel wire, undergoes an initial descaling stage. This crucial phase ensures the removal of rust and impurities, preparing the wire for further processing. The descaling often involves mechanical or chemical methods, promoting the cleanliness and integrity of the steel. Expert manufacturers understand that the quality of this stage significantly impacts the final product’s performance, thus warranting thorough quality checks.
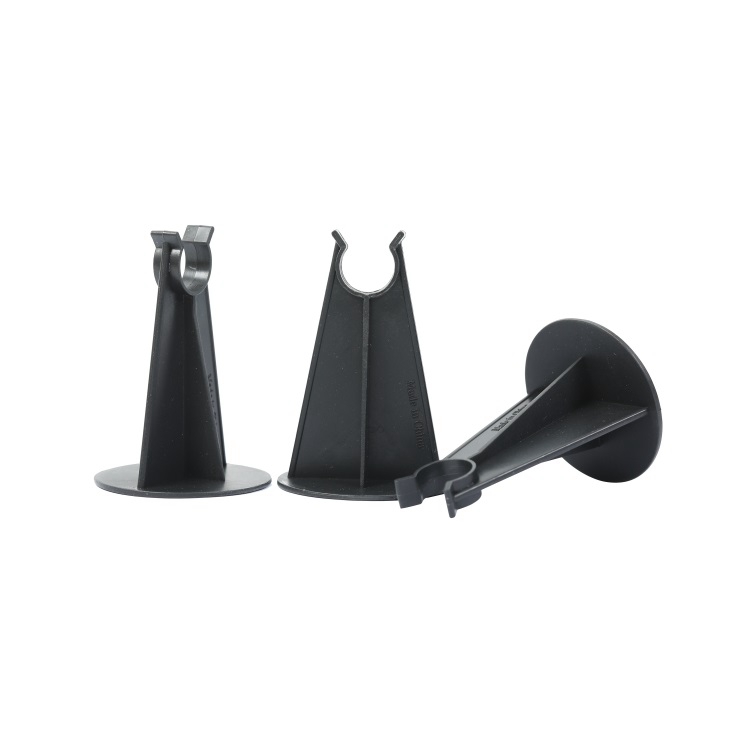
Following descaling, the next phase is wire drawing. This stage reduces the diameter of the steel wire to the desired size, an operation that requires precision equipment to maintain consistent thickness throughout. Expert operators ensure that the wire retains its strength post-drawing, which is critical for the nails’ effectiveness in tough applications. The expertise involved in calibrating the wire drawing machines underscores their role in achieving optimal productivity and quality.
Once the wire is prepared, the nail making stage begins. High-speed nail making machines cut the wire into appropriate lengths, forming the head and sharpening the point in rapid succession. These machines embody state-of-the-art engineering, capable of producing thousands of nails per minute without compromising on quality. This efficiency is crucial for manufacturers who need to deliver bulk orders promptly while maintaining stringent quality standards.
concrete nail producing line
The heat treatment process is another critical phase where the nails' physical properties are enhanced. This stage involves heating the nails to a specific temperature and then cooling them rapidly, a technique that strengthens the steel and enhances its hardness. It is an essential process ensuring that the nails can withstand the stress of being driven into concrete without bending or breaking.
After heat treatment, the nails often undergo a surface treatment process, such as galvanization or phosphating. This step enhances rust resistance, a crucial quality for nails used in construction environments as they are often exposed to the elements. Manufacturers with expertise in surface treatment can offer products that promise longevity and reliability, hallmarks of a trusted brand in the construction industry.
Quality control is a pivotal component across all stages of the concrete nail producing line. Reputable manufacturers implement robust inspection protocols to ensure that each batch meets industry standards and customer expectations. This commitment to excellence not only fortifies the product's credibility but also augments customer confidence, a vital aspect in establishing authority in the industry.
Investing in a state-of-the-art concrete nail producing line is a testament to a manufacturer’s dedication to quality, efficiency, and reliability. It reflects an expertise that reassures clients of the firm’s capability to meet even the most stringent requirements. As industries continue to evolve, the ability to innovate and maintain a cutting-edge production process will distinguish the leaders from the laggards in the field of construction materials manufacturing. Through a blend of genuine experience, expert knowledge, and a steadfast dedication to quality, manufacturers can carve a niche in this competitive industry.