In the realm of construction and manufacturing, the choice of materials plays a pivotal role. Among these materials, 9 gauge galvanized wire emerges as a standout option for its durability, versatility, and corrosion resistance. With years of experience in the industry, I can attest to the advantages of this wire, both from a practical standpoint and as a foundational component in various applications.
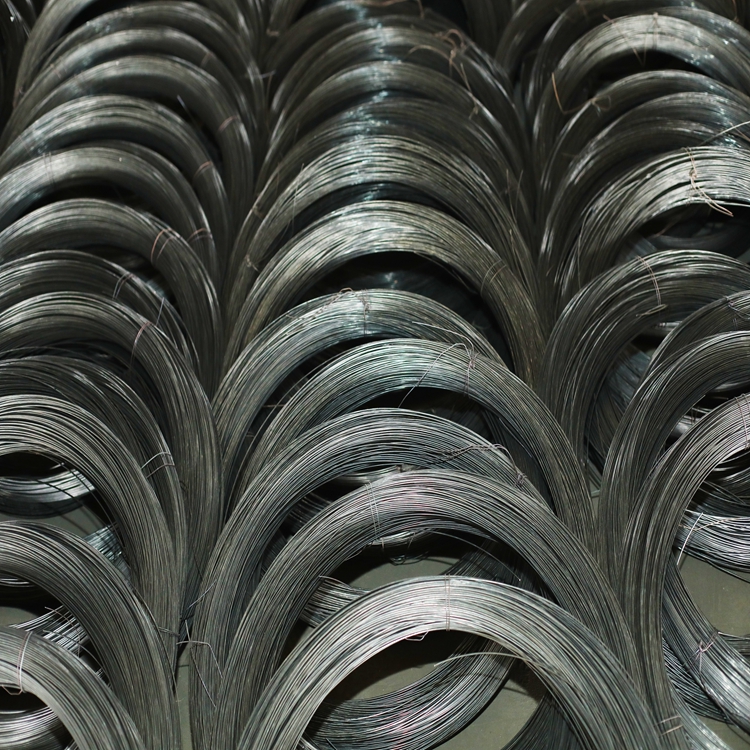
9 gauge galvanized wire is renowned for its robustness.
The term 9 gauge refers to the diameter of the wire, which is approximately 3.76 mm. This thickness provides an optimal balance between strength and flexibility, making it an ideal choice for heavy-duty applications without compromising ease of handling. The galvanization process involves coating the wire with a protective layer of zinc, which significantly enhances its resistance to rust and environmental damage. This feature is particularly beneficial for outdoor applications where the wire is exposed to the elements.
From fencing to artistic creations, 9 gauge galvanized wire exhibits unparalleled versatility. In agricultural settings, it is often used for livestock fencing, as its strength prevents animals from breaching enclosures. Its durability ensures long-term use without frequent replacements, saving both time and resources. In construction, this wire serves as a reliable binding material for reinforcement in concrete structures, offering stability and security.
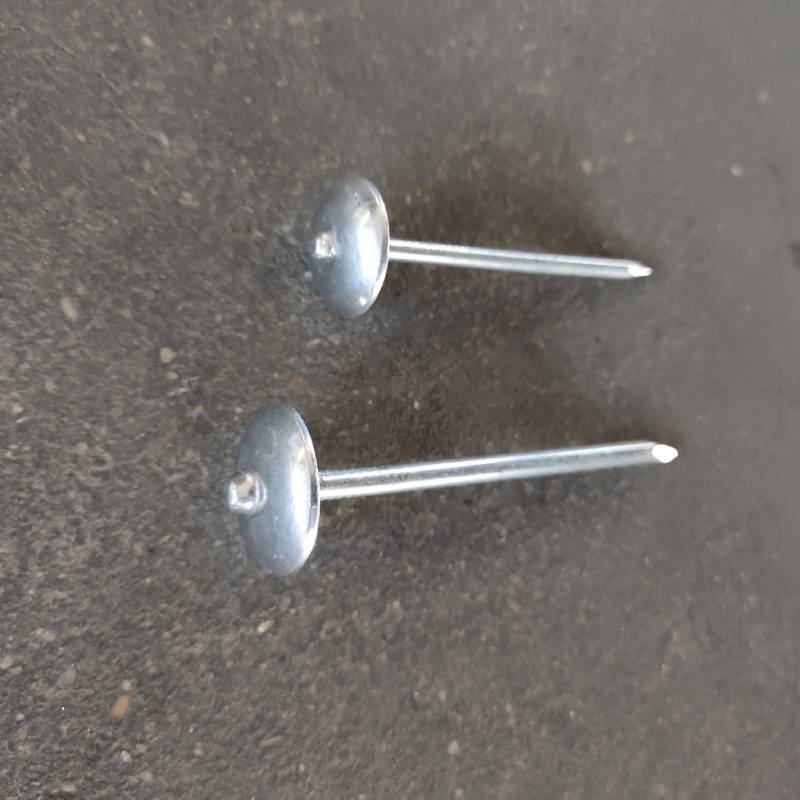
Artists and craftsmen also find value in 9 gauge galvanized wire for its pliability and endurance. Its ability to be shaped and molded without breaking makes it ideal for sculpture and creative projects. Additionally, its corrosion-resistant properties ensure that artworks maintain their integrity over time, even in outdoor installations.
9 gauge galvanized wire
Regarding expertise and technical specifications, selecting the right 9 gauge galvanized wire involves understanding its chemical and mechanical properties. The zinc coating is critical, as it acts as a sacrificial layer that deteriorates before the steel underneath does, thereby prolonging the life of the wire itself. When choosing galvanized wire, it is essential to consider the coating thickness, often measured in microns, as well as the wire's tensile strength, which should be evaluated based on specific application needs.
Trustworthiness in this product arises from its proven track record in various industries. Suppliers often provide detailed documentation and certifications, verifying the quality of the galvanization process and the wire's performance metrics. By sourcing from reputable manufacturers, one can ensure that the wire meets rigorous industrial standards and end-user expectations.
Furthermore, it is essential to understand the market trends and consumer demands for 9 gauge galvanized wire. Recent advancements in galvanization techniques have led to superior, eco-friendly options that utilize fewer natural resources during production without diminishing product quality. This shift not only appeals to environmentally conscious consumers but also adheres to modern industry standards, promoting sustainability in construction and art practices.
In summary, 9 gauge galvanized wire stands as a testament to quality and efficiency. Its distinct advantages are evident across numerous applications, from industrial to artistic. The key to maximizing its potential lies in careful selection, understanding material properties, and ensuring reliable sourcing. For professionals seeking durable, adaptable, and dependable wire solutions, 9 gauge galvanized wire continues to be an exemplary choice, backed by extensive experience, professional endorsement, and an unwavering reputation for excellence.