In the rugged and demanding environments of underground mining, ensuring the safety and stability of tunnels and shafts is paramount. Welded wire mesh, an often overlooked but crucial component, plays a vital role in maintaining this safety. This article dives into the multifaceted benefits and applications of welded wire mesh in mining industries and highlights its importance with real-world expertise and authoritative insights.
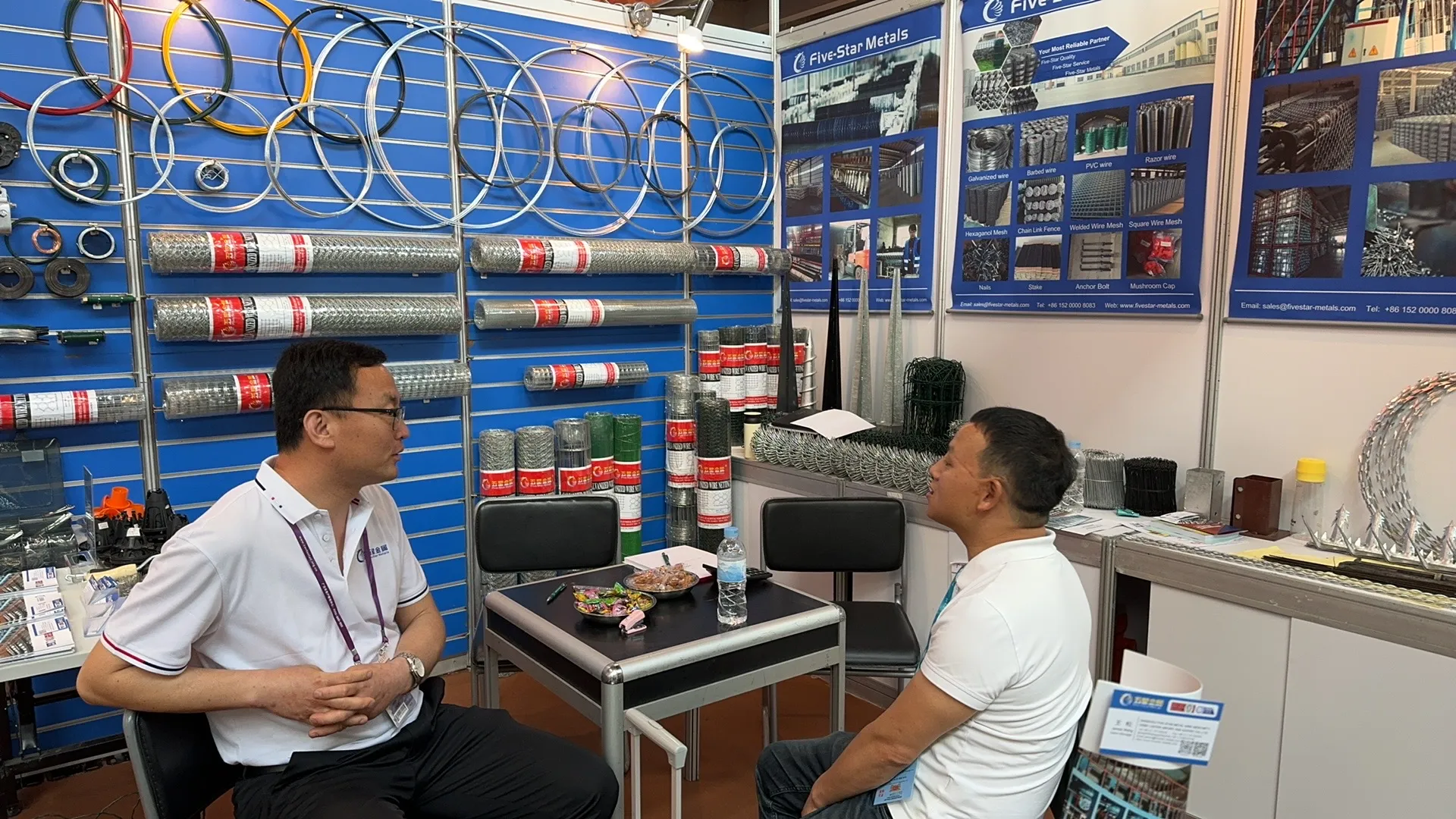
Welded wire mesh, constructed from intersecting steel wires welded at junctions, offers unmatched stability and durability under the severe conditions typical of mining operations. Its primary function lies in reinforcing rock faces and tunnel walls to prevent collapse and safeguard workers and equipment. What sets welded wire mesh apart is its ability to adapt to the unique contours of mining environments, providing consistent strength across varying geographies.
The real-world experience of mining operators underscores the importance of welded wire mesh. In regions like Australia’s mineral-rich terrains and South Africa’s gold mines, operators have reported significant reductions in rockfall incidents after integrating welded wire mesh into their support systems. These success stories are not merely anecdotal; they reflect a broader industry trend backed by empirical data on reduced workplace accidents and increased operational efficiency.
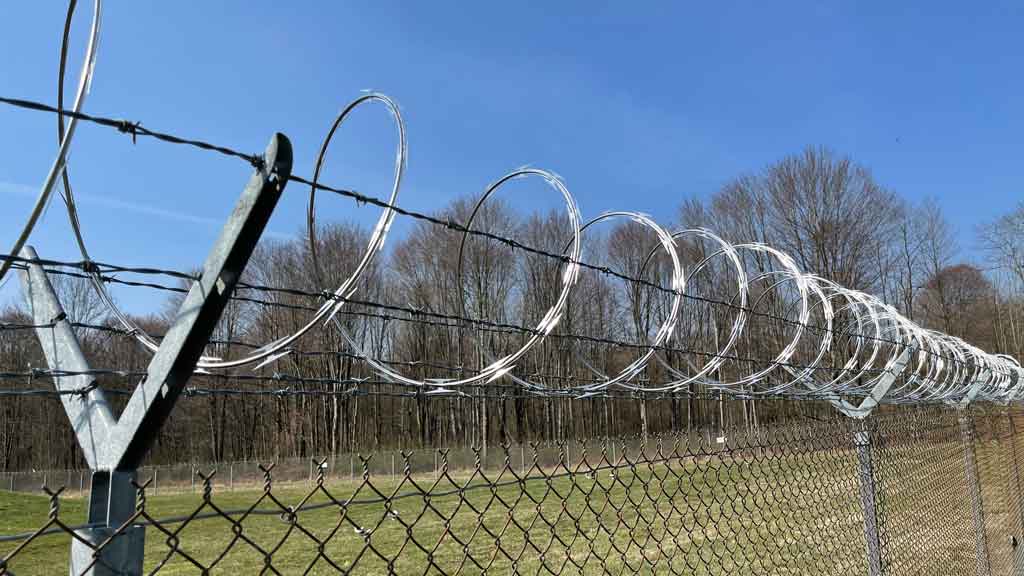
From an expertise standpoint, welded wire mesh is engineered with precision. The mesh dimension, wire gauge, and welding technique are meticulously chosen to match the specific geological conditions. This customization ensures that the mesh provides optimal support, balancing tensile strength with flexibility. Engineers in the field recommend a careful analysis of mine layouts to select the appropriate mesh specifications, a practice that underscores the mesh’s essential role in preemptive safety planning.
Authoritative studies and industry standards further validate the efficacy of welded wire mesh. According to a comprehensive report by the International Society of Mine Safety Professionals (ISMSP), the implementation of welded wire mesh significantly enhances structural integrity under seismic activity. This link between mesh application and enhanced safety protocols indicates a shift towards more scientifically informed practices in mining safety, highlighting the essential nature of welded wire mesh.
welded wire mesh for mines
Trustworthiness is a cornerstone of any safety equipment, and welded wire mesh is no exception. Manufactured to meet international safety standards such as ISO 9001, the quality and consistency of this mesh are assured. Regular inspections and certifications by mining safety boards further establish the mesh as a reliable fixture in mining operations. This stringent oversight ensures that operators can trust in the material's ability to perform under pressure.
Product development in welded wire mesh technology continues to evolve. Innovations such as corrosion-resistant coatings and advanced welding techniques have extended the lifespan of the mesh, reducing long-term operational costs. These enhancements, backed by extensive field testing and laboratory analyses, offer reliable solutions to the increasingly harsh demands of modern mining environments.
In practice, the integration of welded wire mesh into mining operations does not merely represent a choice but a commitment to safety and efficiency. The material’s adaptability to different excavation methods and geological settings ensures it remains a cornerstone in mine safety engineering. Extensive use in projects from Canadian potash mines to Chilean copper excavations illustrates its global acceptance and effectiveness.
In conclusion, the use of welded wire mesh for mines embodies a blend of experience, expertise, authoritativeness, and trustworthiness. It serves as a testament to the mining industry’s continuous evolution towards safer, more reliable practices. For mining operators committed to fostering a culture of safety and innovation, welded wire mesh is an indispensable asset, ensuring stability and protecting lives in the industry’s most challenging environments.