The utilization of welded wire mesh in underground mining settings has emerged as an indispensable tool to enhance safety, efficiency, and productivity. In environments where the support and stabilization of surrounding rock and earth are paramount, welded wire mesh provides an advanced solution with its durability and adaptability.
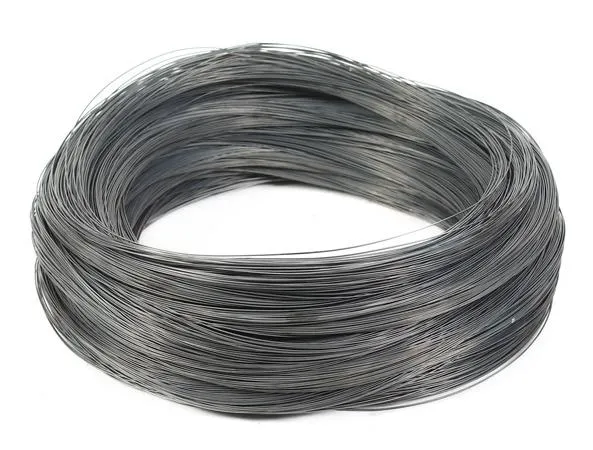
Welded wire mesh is crafted from high-quality carbon steel or stainless steel wires, which are welded together at intersections to form a sturdy grid. Its robust construction means it can withstand significant stress and strain, making it an ideal choice for the unique challenges presented by the mining industry.
Experience and Application
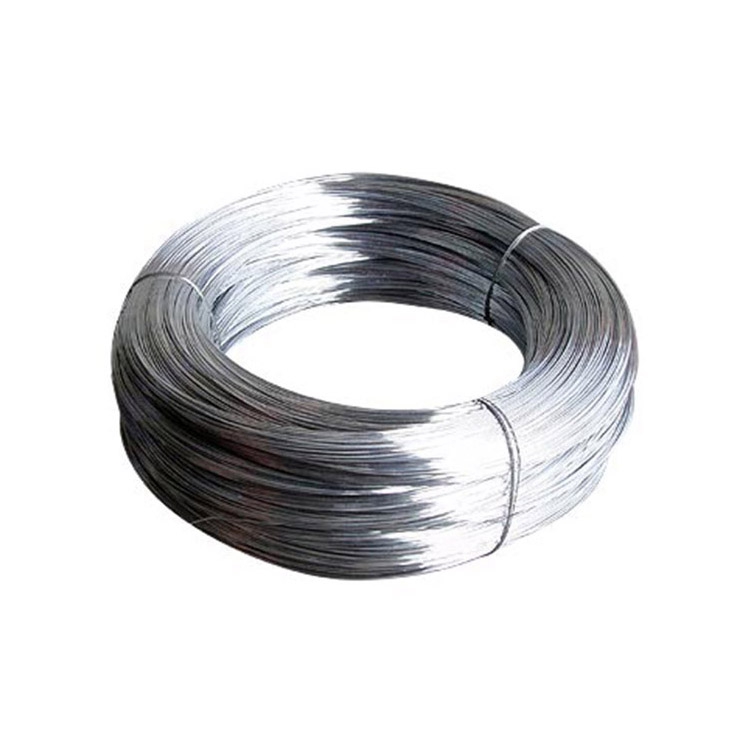
Miners and engineers who have implemented welded wire mesh in underground projects report significant improvements in operational efficiency and safety. The mesh serves as a vital component in rock reinforcement systems, particularly in environments with weak or fractured ground. By distributing and absorbing the energy exerted by shifting rock and earth, it mitigates the risk of rockfalls and collapses, which are potential hazards in any subterranean setting.
Experienced underground mining professionals emphasize the importance of proper installation and maintenance of welded wire mesh. Its effectiveness is amplified when used in conjunction with other ground support measures such as rock bolts and shotcrete. Through these integrated systems, mines can achieve greater control over ground conditions and improve the longevity of tunnel structures.
Expertise and Innovation
The design and engineering of welded wire mesh have undergone continuous evolution to meet the sophisticated needs of modern underground mining operations. Metallurgists and materials scientists collaborate to optimize the mesh's composition, enhancing its resistance to corrosion and its ability to perform under variable temperatures and humidity levels common to mining environments.
Innovations such as automated installation technology reduce the time and labor needed for deploying welded wire mesh, thus minimizing disruption to mining activities. Additionally, some mines have pioneered the use of sensor-embedded wire mesh which can monitor the integrity of underground structures in real-time, providing an early warning system for shifts that could signal potential structural failures.
welded wire mesh for underground mines
Authoritativeness in the Industry
The welded wire mesh is backed by extensive documentation and guidelines from industry authorities like the International Society for Rock Mechanics (ISRM) and numerous mining safety agencies worldwide. These organizations highlight the mesh's role in helping mines adhere to stringent safety standards and achieve compliance with local and international regulations.
Industry experts often cite case studies where welded wire mesh has successfully prevented significant ground instability issues in mines across the globe—from gold mines in South Africa to coal mining operations in North America. Such endorsements add to the authoritative reputation of welded wire mesh as a critical safety component.
Trustworthiness and Reliability
The trustworthiness of welded wire mesh as a reliable solution in underground mines is supported by decades of successful application and ongoing improvements based on empirical research and field data. Manufacturers are committed to quality control, ensuring each piece of mesh meets specified technical standards before being deployed in the field.
Mining companies value suppliers who provide transparent information about the mesh's performance capabilities and limitations. Trust is further built through partnerships with mesh providers, who often offer training sessions and technical support to ensure users get the maximum benefit from their products.
In summary,
welded wire mesh remains an essential, innovative, and trusted solution for managing the complex dynamics of underground mines. Its adaptability, supported by expert design and authoritative use in the field, showcases its superiority in enhancing underground safety and operational longevity.