Selecting the right raw material for manufacturing common nails is an intricate process that involves a deep understanding of metallurgy,
manufacturing processes, and end-user requirements. Experienced manufacturers know that the choice of raw material impacts not only the structural integrity and performance of the nails but also influences production costs and environmental sustainability.
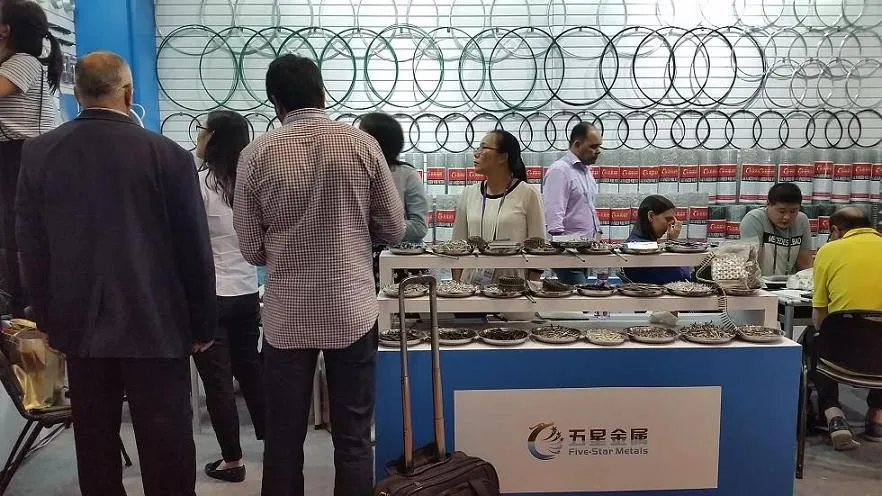
Steel is typically the material of choice when it comes to nail production due to its balance of affordability, availability, and mechanical properties. However, the exact type of steel and its processing can significantly alter the final characteristics of the nails produced. Cold-drawn, mild carbon steel is often favored because it offers sufficient strength and flexibility, ensuring that nails can penetrate various materials without bending or breaking. However, for specialized applications, alloy steels that incorporate elements such as chromium or nickel might be used to enhance corrosion resistance and durability.
Expertise in steel selection involves understanding the carbon content and how it affects properties like hardness and tensile strength. High carbon steel, for instance, is harder and suitable for nails that require superior strength, but it may be more prone to breakage if not properly tempered. On the other hand, low carbon steel offers more flexibility at the expense of holding power. Therefore, a seasoned manufacturer must strike a balance between these attributes to meet the specific demands of their application.
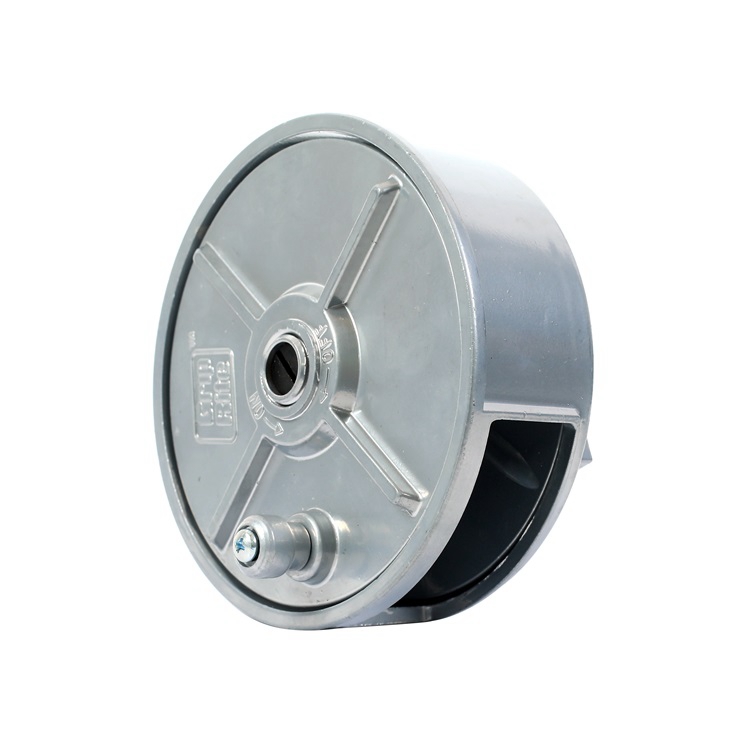
Beyond choosing the right type of steel, the manufacturing process also plays a vital role. Processes such as annealing and tempering are critical in modifying the physical properties of the steel, further affecting the performance of the nails. Annealing involves heating the steel and then slowly cooling it to improve workability, making it easier to draw the nail shapes without compromising their structural integrity. Tempering, on the other hand, involves reheating the nails to a lower temperature and cooling them again, reducing brittleness while retaining strength.
Trustworthiness in the eyes of customers and end-users can also come from the sustainability practices adopted by manufacturers. Environmentally conscious manufacturers might opt for recycled steel, which reduces the carbon footprint of their manufacturing process while maintaining the desirable properties of new steel. Additionally, opting for sustainable practices in energy consumption and waste management can further enhance a company's reputation among environmentally-aware consumers and industry partners.
raw material for common nails
The expertise to produce high-quality nails extends to surface treatments as well. Zinc plating or galvanization is commonly employed to enhance corrosion resistance, essential for nails that will be exposed to moisture. An authoritative voice in the industry will understand the importance of these treatments and ensure that the nails meet stringent industry standards and customer expectations.
Furthermore, advances in technology have introduced automated systems that enhance precision and efficiency in nail manufacturing, ensuring consistent quality and reducing defects. Manufacturers with the ability to invest in such technologies demonstrate a commitment to excellence and innovation, aligning with modern demand for efficiency without compromising on quality.
Performance validation through rigorous testing measures further establishes the credibility of nail manufacturers. Testing for tensile strength, shear strength, and corrosion resistance helps ensure that the nails fulfill their intended purposes reliably. Companies that document and share these testing results enhance their trustworthiness and appeal to markets that prioritize quality assurance.
In conclusion, the production of common nails from raw material selection to finishing is a multifaceted process that demands a blend of experience, expertise, authoritativeness, and trustworthiness. Manufacturers that excel in these areas are more likely to produce nails that stand the test of time, meeting the varied and demanding needs of the construction industry and beyond. By prioritizing quality materials, sustainable practices, and technological innovation, these companies not only fulfill their immediate production goals but also contribute positively to the industry's future.